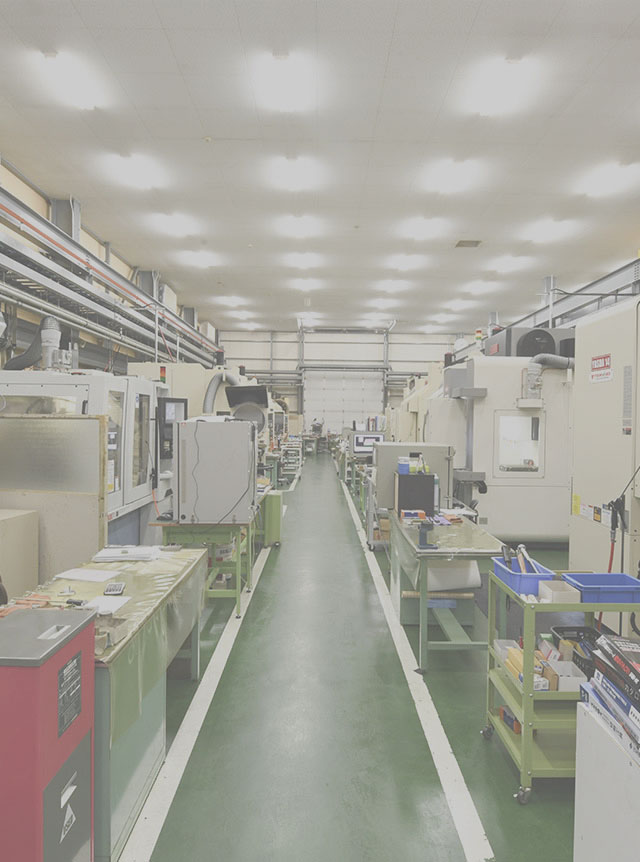
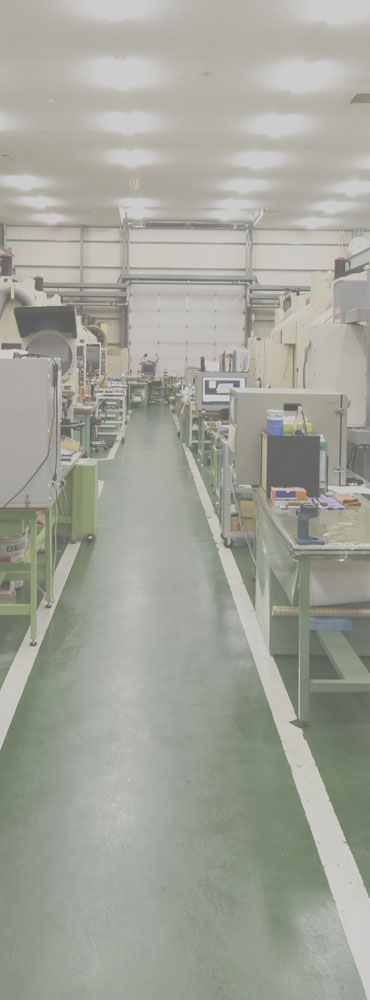
Production system
To respond to diverse needs,
we have constructed a production system
achieved by cooperation between two companies.

In the flow of our business, Step acts as the point of initial contact for client requests—first meeting with the client and working on design and development of molds in consideration of the required levels of accuracy and quality. Depending on the content, Step may work with Futaba Seisakusho to achieve the optimal molds. We have constructed a cohesive, consistent system from order receipt to shipment based on cooperation between the two companies. The entire company is also working to improve product quality, improve process efficiency, and reduce costs.
Responsible for sales and designStep Co., Ltd.
MORE-
Ordering
We have established a flexible ordering system enabling us to respond to all kinds of client requests, including utilization of databases and the Internet as well as participation from the product development stage.
-
Design review
-
Design
-
Production control
-
-
Shipment
Responsible for processing and productionFutaba Seisakusho Co., Ltd.
MORE-
Pre-processing
-
Blade forming
-
Product processing
-
Finish processing
-
Inspection